What is Porosity in Welding: Best Practices for Staying Clear Of Porous Welds
What is Porosity in Welding: Best Practices for Staying Clear Of Porous Welds
Blog Article
The Science Behind Porosity: A Comprehensive Overview for Welders and Fabricators
Understanding the intricate devices behind porosity in welding is critical for welders and fabricators aiming for impressive craftsmanship. As metalworkers look into the midsts of this sensation, they reveal a globe controlled by numerous elements that influence the development of these minuscule voids within welds. From the make-up of the base materials to the complexities of the welding procedure itself, a multitude of variables conspire to either intensify or alleviate the presence of porosity. In this thorough guide, we will certainly unwind the science behind porosity, exploring its impacts on weld quality and introduction advanced techniques for its control. Join us on this trip through the microcosm of welding flaws, where precision meets understanding in the quest of perfect welds.
Understanding Porosity in Welding
FIRST SENTENCE:
Exam of porosity in welding reveals critical insights into the honesty and top quality of the weld joint. Porosity, characterized by the presence of dental caries or spaces within the weld metal, is an usual concern in welding procedures. These voids, otherwise effectively dealt with, can endanger the architectural integrity and mechanical homes of the weld, bring about possible failings in the ended up item.
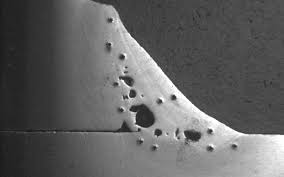
To detect and measure porosity, non-destructive testing approaches such as ultrasonic testing or X-ray inspection are commonly used. These strategies permit the identification of internal problems without endangering the stability of the weld. By analyzing the dimension, form, and distribution of porosity within a weld, welders can make enlightened choices to boost their welding procedures and achieve sounder weld joints.

Aspects Affecting Porosity Formation
The occurrence of porosity in welding is affected by a myriad of factors, varying from gas protecting effectiveness to the complexities of welding parameter settings. One important factor contributing to porosity formation is poor gas securing. When the shielding gas, normally argon or CO2, is not properly covering the weld pool, atmospheric gases like oxygen and nitrogen can pollute the molten metal, leading to porosity. Furthermore, the cleanliness of the base products plays a substantial function. Contaminants such as corrosion, oil, or wetness can evaporate during welding, developing gas pockets within the weld. Welding criteria, consisting of voltage, present, take a trip speed, and electrode type, also influence porosity formation. Making use of incorrect settings can produce too much spatter or warmth input, which consequently can lead to porosity. In addition, the welding technique employed, such as gas metal arc welding (GMAW) or shielded metal arc welding (SMAW), can influence porosity formation due to variations in warmth distribution and gas insurance coverage. Understanding and managing these aspects are essential for minimizing porosity in welding operations.
Impacts of Porosity on Weld High Quality
Porosity development significantly endangers the architectural honesty and mechanical homes of welded joints. When porosity exists in a weld, it develops voids or cavities within the product, lowering the general strength of the joint. These spaces work as stress and anxiety focus factors, making the weld a lot more vulnerable to fracturing and failure under lots. this article The visibility of porosity likewise compromises the weld's resistance to corrosion, as the caught air or gases within the voids can respond with the surrounding setting, causing degradation in time. In addition, porosity can impede the weld's capability to stand up to stress or influence, further jeopardizing the general quality and integrity of the welded framework. In essential applications such as aerospace, vehicle, or structural building and constructions, where safety and security and resilience are paramount, the damaging effects of porosity on weld quality can have serious effects, stressing the significance of minimizing porosity with correct welding techniques and procedures.
Strategies to Decrease Porosity
To enhance the quality of bonded joints and make certain structural honesty, welders and makers use certain strategies focused on lowering the development of spaces and cavities within the material during the welding procedure. One efficient approach to minimize porosity is to guarantee correct material prep work. This consists of detailed cleaning of the base steel to remove any kind of contaminants such as oil, grease, or dampness that might contribute to porosity formation. Additionally, utilizing the ideal welding parameters, such as the proper voltage, existing, and take a trip speed, is vital in stopping porosity. Keeping a consistent arc size and angle during welding additionally helps Extra resources in reducing the probability of porosity.

In addition, selecting the best protecting gas and maintaining proper gas flow rates are vital in lessening porosity. Using the suitable welding strategy, such as back-stepping or employing a weaving motion, can likewise aid disperse warmth evenly and reduce the opportunities of porosity development. Guaranteeing proper ventilation in the welding setting to eliminate any kind of possible sources of contamination is essential for attaining porosity-free welds. By carrying out these techniques, welders can effectively reduce porosity and produce top quality bonded joints.

Advanced Solutions for Porosity Control
Implementing sophisticated innovations and innovative techniques plays a crucial role in achieving superior control over porosity in welding processes. In addition, using sophisticated welding strategies such as pulsed MIG welding or modified ambience welding can also assist reduce porosity concerns.
Another innovative remedy entails the use of innovative welding equipment. Using tools with built-in attributes like waveform control and sophisticated power resources can boost weld top quality and minimize porosity dangers. The execution of automated welding systems with accurate Our site control over parameters can significantly minimize porosity defects.
Additionally, integrating advanced monitoring and evaluation modern technologies such as real-time X-ray imaging or automated ultrasonic testing can aid in detecting porosity early in the welding procedure, permitting prompt corrective activities. On the whole, incorporating these sophisticated remedies can greatly enhance porosity control and enhance the general top quality of welded parts.
Final Thought
In final thought, comprehending the science behind porosity in welding is important for welders and producers to produce top notch welds - What is Porosity. Advanced services for porosity control can additionally boost the welding procedure and make sure a strong and trustworthy weld.
Report this page