What is Porosity in Welding: Secret Variables and Their Impact on Weld Quality
What is Porosity in Welding: Secret Variables and Their Impact on Weld Quality
Blog Article
The Scientific Research Behind Porosity: A Comprehensive Overview for Welders and Fabricators
Comprehending the elaborate devices behind porosity in welding is crucial for welders and makers aiming for flawless craftsmanship. From the make-up of the base products to the complexities of the welding procedure itself, a wide variety of variables conspire to either aggravate or relieve the presence of porosity.
Comprehending Porosity in Welding
FIRST SENTENCE:
Assessment of porosity in welding exposes important insights into the honesty and high quality of the weld joint. Porosity, identified by the presence of tooth cavities or voids within the weld steel, is an usual concern in welding procedures. These voids, if not appropriately resolved, can endanger the structural stability and mechanical residential or commercial properties of the weld, causing potential failures in the ended up product.
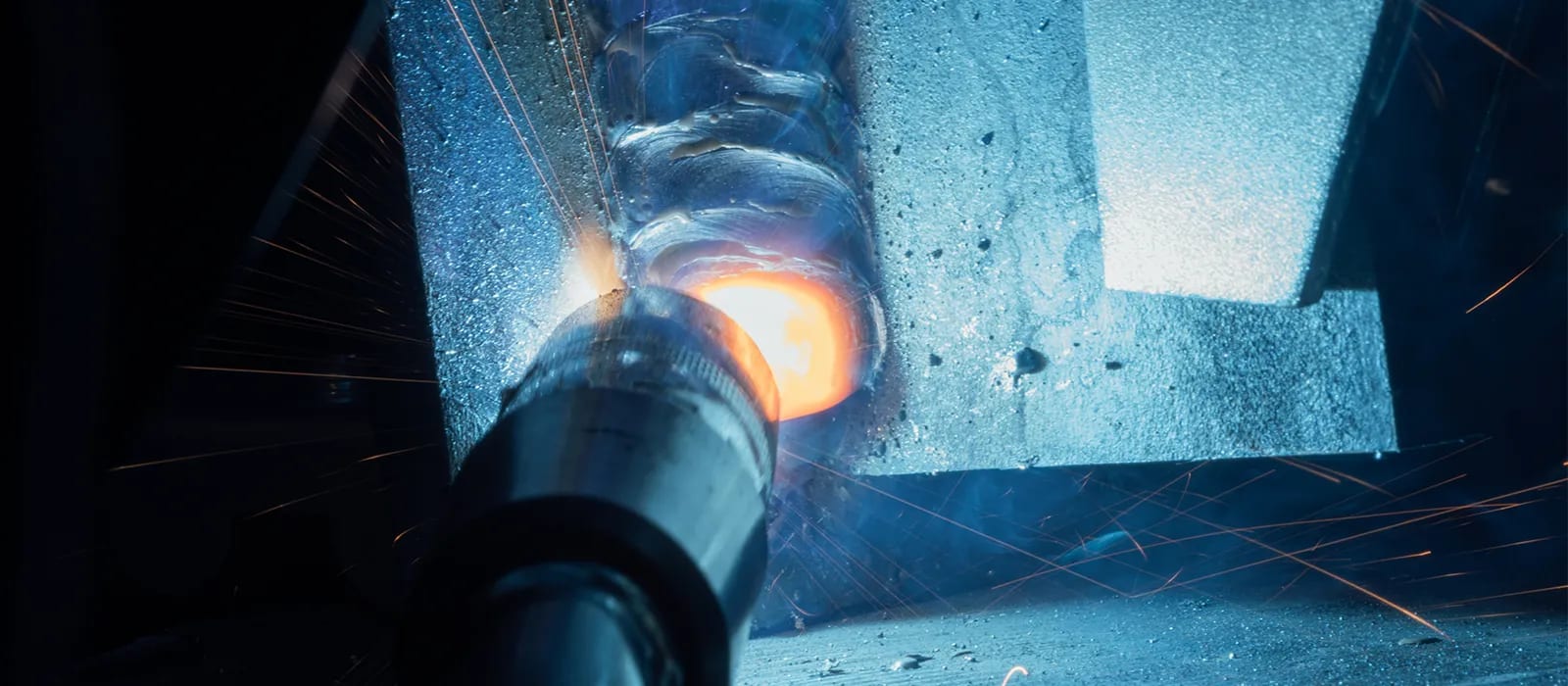
To detect and quantify porosity, non-destructive testing techniques such as ultrasonic screening or X-ray evaluation are frequently used. These methods enable the recognition of inner issues without jeopardizing the honesty of the weld. By analyzing the size, shape, and distribution of porosity within a weld, welders can make informed decisions to improve their welding processes and attain sounder weld joints.

Elements Affecting Porosity Development
The incident of porosity in welding is affected by a myriad of elements, ranging from gas securing effectiveness to the details of welding specification setups. Welding specifications, consisting of voltage, current, take a trip speed, and electrode type, additionally effect porosity development. The welding technique used, such as gas steel arc welding (GMAW) or protected metal arc welding (SMAW), can influence porosity development due to variations in warm circulation and gas coverage - What is Porosity.
Impacts of Porosity on Weld Quality
The visibility of porosity also damages the weld's resistance to deterioration, as the caught air or gases within the spaces can react with the surrounding environment, leading to degradation over time. In addition, porosity can impede the weld's capacity to stand up to pressure or effect, additional threatening the total top quality and integrity of the bonded structure. In vital applications such as aerospace, automobile, or structural buildings, where security and resilience are paramount, the detrimental results of porosity on weld high quality can have severe consequences, highlighting the value of reducing porosity through correct welding methods and treatments.
Methods to Minimize Porosity
Additionally, making use of the suitable welding specifications, such as the proper voltage, current, and travel speed, is vital in protecting against porosity. Preserving a constant arc size and angle throughout welding additionally helps decrease the probability of porosity.

Making use of the proper welding method, such as back-stepping or employing a weaving activity, can additionally assist distribute warmth uniformly and decrease the opportunities of Click Here porosity formation. By executing these methods, welders can properly minimize porosity and produce premium welded joints.

Advanced Solutions for Porosity Control
Carrying out cutting-edge innovations and cutting-edge methods plays a pivotal function in attaining exceptional control over porosity in welding procedures. Additionally, using sophisticated welding strategies such as pulsed MIG welding or changed ambience welding can also assist reduce porosity issues.
One more innovative solution involves making use of sophisticated welding tools. For instance, utilizing devices with integrated attributes like waveform control and advanced source of power can improve weld top quality and decrease porosity threats. The implementation try here of automated welding systems with accurate control over parameters can dramatically decrease porosity issues.
Furthermore, incorporating sophisticated tracking and assessment innovations such as real-time X-ray imaging Home Page or automated ultrasonic screening can help in finding porosity early in the welding procedure, enabling immediate corrective actions. Overall, incorporating these innovative options can significantly improve porosity control and improve the total top quality of bonded parts.
Final Thought
Finally, comprehending the science behind porosity in welding is important for welders and makers to create top notch welds. By determining the elements affecting porosity development and executing techniques to decrease it, welders can enhance the general weld quality. Advanced remedies for porosity control can additionally improve the welding procedure and make sure a strong and reliable weld. It is essential for welders to continuously enlighten themselves on porosity and carry out best techniques to achieve optimum results.
Report this page